Tips to Optimize Design for CNC Machining Parts
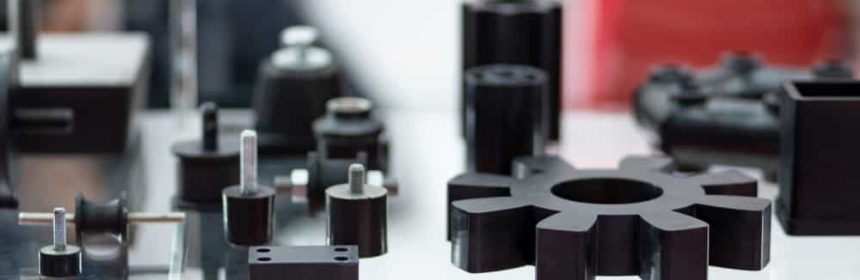
CNC machining is used by a number of plastic and metal part manufacturers owing to the accuracy and volume it can offer irrespective of the design complexity, shape, and size of the product. With CNC machining you can accurately drill holes of the same size, form, cut, grind, mill, tap, and perform several other techniques to get the plastic or metal sheet in the required shape and size. Also, this same process can be followed to make thousands of parts of the same type with same accuracy and at a high speed. Prototyping has further added to this boon. These are some aspects why CNC machining has evolved and gained traction over the years. However, it is equally important for a design engineer and technician to get the most out these machining techniques. This post offers some tips on optimizing the design for CNC machining parts.
Know How You Can Optimize Your Part Design Vis-à-vis the CNC Machining Techniques
- Irrespective of the versatility and flexibility of CNC machining techniques, there are some restrictions or limitations of technique with respect to the material, precision, and so on. Ensure you know all these limitations beforehand so that you can design the part accordingly and find the best possible way out.
- While you may have machines with multiple axes catering to more than one job at a time, they need to be pre-programmed correctly. Else, there could be a loss of productive time, and it would defeat the very purpose of these versatile machines. So proper programing and scheduling are essential to get the right part on time.
- As an organization, you must focus on quality as well. Adopting practices such as Lean, kaizen, or Six Sigma certainly helps identify defects beforehand and improve quality, accuracy, and productivity.
- DFM or design for manufacturing is some much recommended program players may want to adopt for best practices in designing.
- While automation and technological advancements play a key role in improving part design and making the part in bulk volumes, your focus and attention to detail are just as important.
- Adopting the right inspection methods which can be executed right from the first stage of manufacturing is crucial. This includes manual inspection as well.
- Reducing waste is one of the benefits of this technique; however, the team must be able to choose the right tools and techniques to achieve the same.
- While there are no standards for applying the right CNC machining techniques, its tools and machines are ever evolving. You need to adapt to the advanced traits the new tools offer.
- There are some aspects you must be careful about while designing, such as the inner edges or the wall thickness. The wall thickness depends upon the material, wherein for plastics it is usually 1 mm minimum and for metals it could be 0.5 mm. Likewise, when designing inner edges, consider the corner radii and the cavity depth.
- The small and intricate features in the design demands more of the machining technique. You can use special carving and drilling tools for the same.
- There may be some requirements with tight tolerances. This means a tolerance or variation of plus or minus 0.005″ for metal and 0.01″ for plastic is most likely permissible. It is crucial to ensure your machines and tools will help you achieve the required tolerances. Do not use default tolerances; instead discuss with the client about their tolerance requirement.
If you are an OEM making plastic or metal parts or products and need fabrication services, ensure you partner with the right service provider. They must understand your requirements and assist you choosing the right machining techniques for your product design. Brogan & Patrick offers various types of CNC machining techniques for all your metal and plastic applications.